How Steve Thayer started Thayercraft
About Thayercraft
History of Thayercraft Inc by President and Founder Steve Thayer
I've been around fiberglass cloth since I was a young boy. My father was in the heating business and he saw the huge loss of heat in homes in the early 60's. This gave him the inspiration to go into the insulation business. He started with grinding newspapers to make the cellulose type insulation. My brother and I helped carry string tied bundles of newspapers to him as he fed the diesel powered hammermill when I was 8 and my brother 7. Not long after we would feed the grinder by ourselves. We had a small steel hopper with holes to feed the boric acid fire retardant at the opening of the grinder on the newspaper. The ground insulation went through the blower on the side of the grinder through pipes attached to the side of the bed on an old 1954 chevy box truck. We would use stick matches to do our own burn tests on the boric acid treated ground newspaper cellulose insulation . My father had mounted an insulation feeder/blower under the floor at the back right corner of the bed of the truck. My brother and I would go with him to insulate and feed the ground cellulose insulation in the feeder while he blew attics of houses. Later on we also did the walls of old houses taking the wood siding off and blowing the cellulose in the walls. A few years after making cellulose insulation my dad got the idea of making it out of fiberglass and found a source of waste fiberglass to grind for the new fiberglass insulation. He found a fiberglass textile manufacturing company that had the leftover fiberglass cloth pieces from where they would start the rolls on the cores or start it in their finishing system. All this cloth was woven from glass yarn that had filaments in the 5 to 13 micron range with most being 7 to 9 microns. I believe I was about 12 or 13 years old or somewhere in that range when we started bringing in the bales of fiberglass and grinding these short pieces into insulation.
The advantage of the blowing insulation we made from the surplus fiberglass scrap pieces over the type you find being used now is that our fiberglass blowing insulation was made from the true monofilament glass fibers. True monofilament just means the glass fibers had a completely consistent thickness from one end to the other. The fiberglass blowing wool you commonly find in the big hardware stores is made from the spun glass fibers where the molten glass is pulled from a drum and go from thick to a thin point and are coated with some kind of dye to give it color. The glass fibers used in fiberglass cloth are perfect true rods. They range in diameter from 5 to 13 microns depending on the properties of the fabric desired. Glass from perfect true rods is considered harmless to the human body by shape and in its composition. The ends are an irritant of course. Trials had been done in consideration of using this true monofilament glass as surgical thread but failed to pass the test because of it vulneribility to breakage. Glass fibers have good tensile strength but they are glass and do break when bent past their limit. This, however, made some of the best insulation in the world - if not being so itchy of course. The same yarn is used in making the dense sound proof insulation mat the weaver mentioned above, and some other fiberglass weavers, produce.
I had made enough money helping my father in the insulation business to buy an old rough 1968 or 69 Bultaco Pursang 250 motorcycle by the time I was 14 or 15 or somewhere in that range. He did the negotiating on it and got it cheap. My first fiberglassing was for a high school project where I did a copy of one of the fiberglass side covers from the Pursang. Finding a time when my father wasn't around I went out to his old shed, used regular parafin wax as a release agent, some of the tooling cloth I found in one of the bales and regular polyester resin. It came out kind of junky but was good experience. I've loved fiberglass ever since.
As time went by the weaver was supplying more bales of fiberglass than my father was able to convert to insulation. They had started paying him on a monthly basis to take the bales. With my brother driving mostly they were hauling tractor trailer loads of the bales and just putting it outside on the property in Thomasville NC. My brother started driving much younger than one could openly delare here so let's just call it co driving. They continued hauling tractor trailer loads of the bales throughout the 70's. When I was 18 or in that range me and my father didnt really get along so well, or anytime ever for that matter, and I had moved on to other things working at a local plastics company, working on the pipeline here in NC then moved to Florida working for a crooked insulation company that fired me for putting too much insulation. I was used to working with my father that would put one third to almost twice what he was supposed to in attics. Me refusing to put just an inch or so and just the 6" close to the hole got me fired. After that I went to work on a dredge in the Gulf of Mexico. My father and I seemed to get along better the further away we were from each other. So we talked and he decided it would be good for me to move back to NC and help in his business again. Not being able to get a rythm going working with my father in the insulation business I started sending letters with fiberglass samples to sign companies and hobby shops. I went two years to the local community college and got an Associate of Science degree during this time. I sold about 30,000 yards of styles 104, 106 and 1080. I also sold a material that was originally intended for theater screens as banner material. I hand rolled this cloth to 50 yard rolls, took them to a local lumber company, and cut them down to 37.5" and 54" widths and sold the 75" as is. All this cloth was one one tractor trailer. Big rolls of 7678 75" and all the lightweight cloth was on one trailer. I used to spray silicone and used the opened boxes laying out cardboard making a path to the back of the trailer and slid the rolls out to a backhoe bucket. Some of these rolls weighed 700 - 1000 pounds. I would carry the rolls in the buckets to a little 24x22 ft block building that I re rolled the rolls for sign cloth. I used to come home from Cullowhee NC where I was going to Western Carolina University and come home to roll cloth. I had sold about 20,000 yards to K&B Mfg for $0.60/yd for $12,000 total. The deal was with the agreement that I would give my father half or $6,000. With that he said "for that you can have all the rest of the fiberglass cloth in all the trailers and the rollers" - never anything in writing from him though. If you asked if you could get something in writing he would get mad. So K&B being slow to pay even over the 30 days of the agreed upon Net 30 he ran me off again and moved back to Florida settlng in Palm Bay. I was down there when K&B finally paid. I mailed him his half. I stayed in Palm Bay and sold cloth to the surfboard companies in Melbourne for a while back and forth to NC to get cloth.
Going back in time a little my father had quit bringing in the fiberglass bales sometime in the late 70'. He had kept lots of the bales dry in his A frame Buidling and another he built and some was covered with canvas tarps outside. Eventually he ran out of what had been kept dry and was trying to dry some by constructing a big drum dryer out of a galvanized culvert. This dryer only dried about $60 worth an hour not even economically practical at all. One morning I went for a 4 mile swim and had the inspiration to just call weavers and see if anybody had any material to sell. I called JPS in Slater, SC, discussed some possible fiberglass mat trim they had to get rid of, arranged a meeting with them between myself and my father. Afterward on the day to meet with them I had to nearly beg my father to go ahead and go to meet with them. When we got there he wanted to go to the landfill to see what they were hauling there but I insisted we had a meeting and should just go to see them at their office. When we all met I let him do the talking, which there wasnt anything to negotiate really, they wanted to get rid of it, he talked them into 2 cents a pound or so. So with the help of one of my father's friends he let me drive his truck, get my CDL's, and haul the bales of the mat trim in to grind into nsulation. When I would pick up at Slater I got them to sell me some of the over run cloth also. I made some contacts and used to sell this to Fiberglass evercoat to add to their bondo. The milled fiberglass we made out of the much finer filament size versus the big companies was stronger by weight but hard to mix in but I was getting this going and me and my father fell out and he pretty much ran me off and I moved to Florida for a while. I kept selling fiberglass cloth from the Opa-Locka airport, selling aircraft parts and doing some aircraft fiberglass repair. I had bought some cloth back from CW Myers he had sold some to earlier. I used to pull a U-haul trailer back and forth to Miami. After a couple of years selling to surfboard companies in Melbourne and selling out of the Opa-Locka airport my father wanted me to come back to NC so I did.
Around 1992 I did a bunch of composite panels, actually sold some Kevlar midget panels and built a swimming tank on an old, old, semi trailer at my father's place. Building the swimming tank gave me a lot experience with many types of fiberglass weaves - woven roving, fabmat, 3733, 7533 and happened to have a bunch of 1597 40 ounce tooling cloth. I used 7781 in the doors. This swimming tank had a TV in it and I could strap myself in and do the american crawl or just lay back and watch tv - really cool. During that time I was bringing in a bunch of surplus woven roving and re packing, separating and selling to Boat builders. This was about when I got my CDL's. On my first trip with just the CDL permit I hauled a load of woven roving to a company in South Carolina and then to a big boat builder in Washington NC.
I kept on buying cloth, rerolling it, sending letters through the 90's. I grew and grew and was renting three different warehouses by 1994 paying $4700 a month. I got lucky and bought a lot of cloth cheap and resold it to Circuit Board companies and other large manufacturers, lived poor, saved the most of the money I made, went to the auction when the former Alma Desk Co was being sold in 1995 and wound up buying it pretty cheap. We've done a lot of work to the 3.5 acre 350,000 square foot facility here over the years and now have over 3,000,000 yards of cloth in here. I incorporated the company in 2007 changing the name from Thayercraft Industries to Thayercraft Inc. The photo at the bottom is our facility here in High Point NC
We do the best we can to have a good variety of fiberglass cloth for many different applications. Though we have a huge building we don't have a lot of people working. This keeps our costs down that we pass along to you. A big portion of the cloth we ship out is re rolled on 2" schedule 40 PVC pipe. We got started doing this about 8 years ago. There's a couple of reasons for this. A lot of the fiberglass cloth we sell is tightly woven and very unforgiving when it comes to rolling it without getting wrinkles. The PVC pipe costs more but it insures the cloth is not wrinkled. For wider widths this keeps it from getting crushed if the roll endures bending loads. Though it cost more to do it this way we still sell the cloth cheap. We don't fold cloth. We did do some 3 yard packs back around 2004 that came about from some customer requests but what we knew before and were assured of after the fact is that creases are created that will not come out when you laminate with cloth that's been folded. We still have some international customers that want us to fold fiberglass cloth to save shipping costs but we refuse to do it knowing it will be hard for them to work with later. The re rolled rolls are rolled on a pretty primitive type apparatus where the big roll is rolled to the smaller one without touching anything and, for the most part, is not touched by our hands. Except for the beginning and very minimal at the end which is the beginning of the roll for you.
We have sufficient material handling equipment including several forklifts and can ship truck load quantities or small individual rolls. We take the upmost care in inspecting everything we ship out making sure the cloth is good and it's all well packed for the journey from us to you. We don't have a bunch of money tied up in expensive equipment and have been very frugal in all our expenses passing all this along to you. We have a tremendous inventory and huge field of experience with fiberglass cloth.
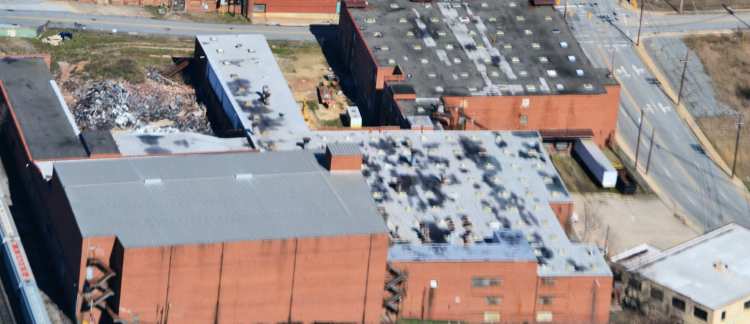
Aerial photo of Thayercraft's facility I bought in the 90's at bankruptcy auction. Building sitting vacant for years, was being vandalized, all electric line copper stripped, homeless people living in it and being frequented by local gangs. On the bottom right of the photo is the building where the Fli-Back paddle was made back in the 50's. We had our office there at one time but now is undergoing a slow renovation. To the top sections of the photo you can see parts what used to be older wood building I took down myself with the excavator with helpers movin the old wood to inside newer buildings. This has been a huge sacrifice of my time, money and energy in rennovating it and keeping it secure. The huge building on the lower left next to the railroad track is the five story building that was the warehouse section of the former Alma Desk Company. We have fiberglass cloth on the first two floors and when we can sell enough fiberglass cloth fast enough will get the elevator working and use some of the upper floors. The buildings with three floors in between the tan Fli-Back building with the windows and the building in the upper right are loaded with fiberglass cloth. We use most of the building for organizing the fiberglass cloth we sell.
Photo immediate right is me on the left, my wife Julissa on the far right, My Mother Valeria sitting, and my two daughters Julie Rose standing and Bridget Thayer. Far right is main packing area for light weight cloth re rolled rolls
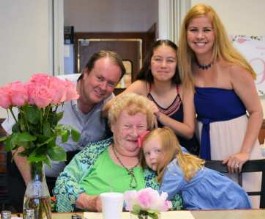
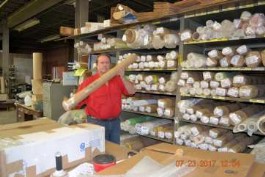
To the immediate right is me doing demolition old finish line Alma Desk Bldg with newer 5 story building behind. Far right is
me carrying roll of cloth. Normally just wearing much grungier clothes.
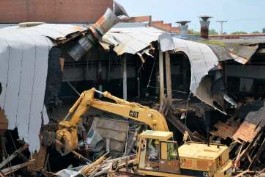
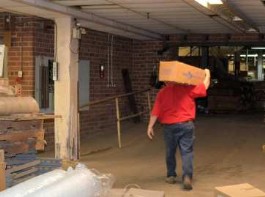
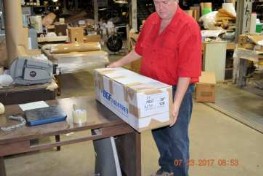
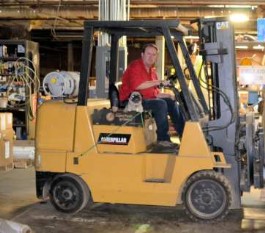
